WORLD OF WHISKY
Green bottles
The Scotch whisky industry has made steps to reduce its carbon emissions, but still has a long way to go – with the added pressure of ensuring that new technologies don’t impact on spirit character. Gavin D Smith takes stock of whisky’s low-carbon future
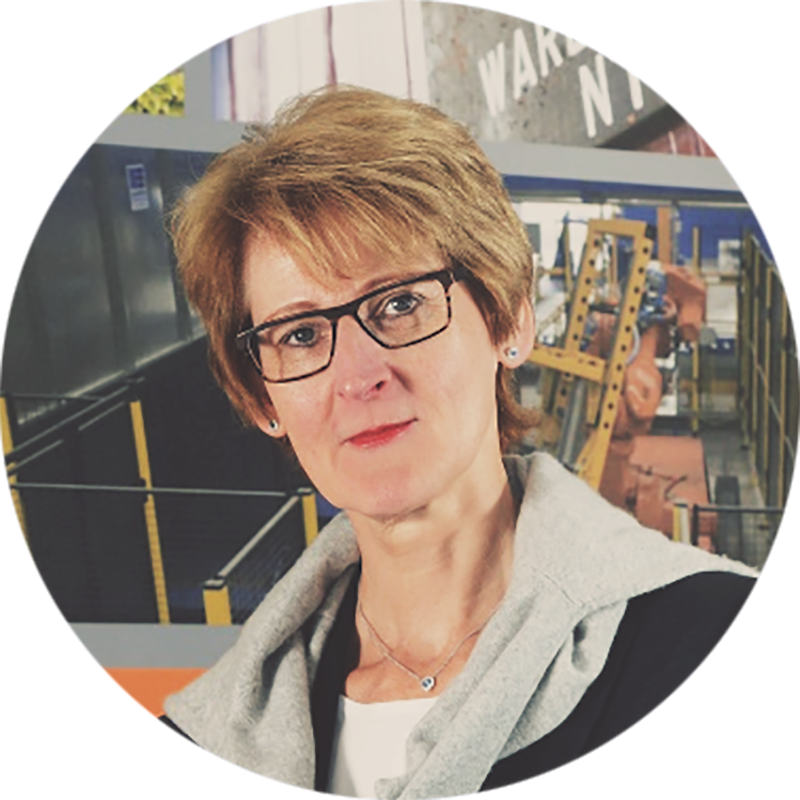
“While companies have already invested in existing technologies such as biomass and anaerobic digestion, it is important that the UK and Scottish governments provide policy certainty on the implementation of new technologies”
DAGMAR DROOGSMA
We’re very comfortable discussing whisky’s aromas, flavours and singing the praises of the single cask. But with every bottling there’s a less sexy subtext about the industry’s environmental impact, and what it’s doing to counter its carbon emissions.
“The uncomfortable fact is that spirit-making is a highly energy-intensive process,” says Gareth Roberts, distillery architect and consultant from Organic Distilleries in Helensburgh, the firm behind the creation of the new distilleries Lindores, Ardnamurchan and Nc’nean.
“Broadly speaking, it takes around one litre of fuel oil to produce each litre of pure alcohol. And there is a lot of spirit made in Scotland, so whisky may be one of our great production successes, but it is also one of our largest carbon producers. Whisky production is around seven times more energy intensive than gin production.”
STRINGENT TARGETS
There are potential solutions to that problem, and the Scotch Whisky Association (SWA) has set out stringent targets for cutting carbon emissions in its Environmental Strategy.
“Collectively, the sector has made significant improvements to our environmental impact since the SWA first launched our Environment Strategy in 2009,” says Dagmar Droogsma, director of industry at the SWA. “The industry now sources over a quarter of primary energy use from non-fossil fuel sources; water efficiency has improved by 22 per cent since the 2012 base year – more than double the 10 per cent improvement target; and only one per cent of waste is now being sent to landfill, down from four per cent in 2016.”
There’s much further to go, however. In June 2020, the SWA published a report setting out how the Scotch whisky industry can achieve net zero emissions by switching from fossil fuels to clean energy.
“While companies have already invested in existing technologies such as biomass and anaerobic digestion, it is important that the UK and Scottish governments provide policy certainty on the implementation of new technologies such as hydrogen and high-temperature heat pumps [essentially recovering energy from hot water and turning it into steam],” says Dagmar.
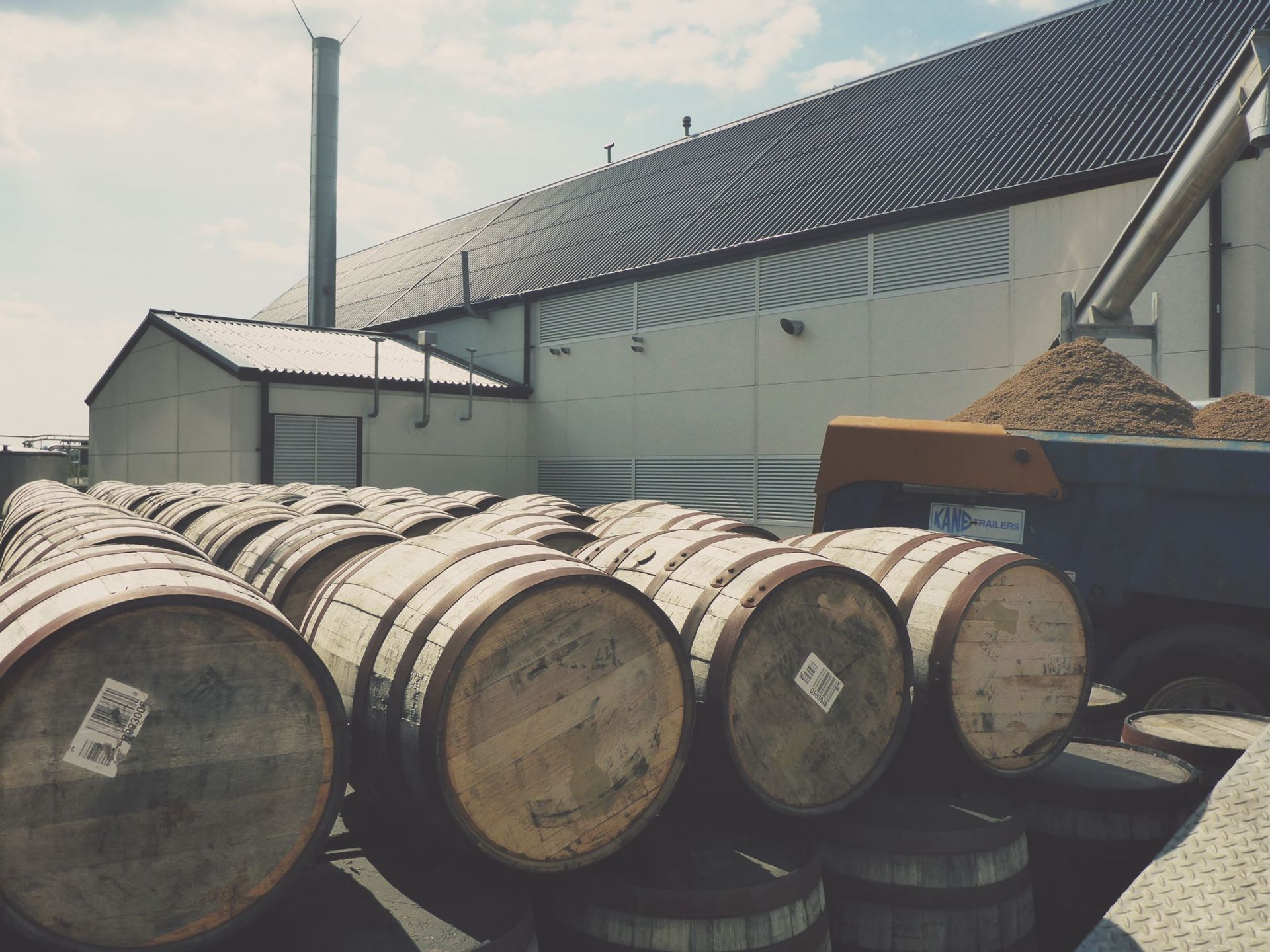
ABOVE: Ardnamurchan distillery’s biomass process. Image courtesy of Organic Distilleries
FLEXIBLE SOLUTIONS
Apart from the policy certainty that Dagmar talks about, other challenges facing distilleries depend on a variety of factors, including the age of the plant and its location.
Shane Healey, distilling director for Whyte & Mackay, emphasises the need for flexibility. “It’s a case of finding the option that fits each site best from what is available,” he says. “Every company will find its own best way of getting to carbon neutrality. We have converted two of our five distilleries from heavy fuel oil to liquified petroleum gas (LPG), which gives us a 30 per cent reduction in carbon emissions. But we really need carbon-neutral fuel sources. Each location needs a different answer. Take Jura, for example, which is very remote, and where we are currently using oil at the distillery. There is lot of tidal power and wind farms in the area, but the technology is just not quite developed there to enable us to use it.”
Pointing out that there is a great deal of woodland on the mainland of Kintyre, not far from Jura, Shane says: “This makes biomass one option, and we’ve been evaluating that. Compressed natural gas is another possibility. Two of our other sites are on the national gas network, so we use gas there, and compressed gas goes to the other two. We’re also working on anaerobic digestion.”
Gareth Roberts echoes Shane’s need to opt for site-specific solutions. “Renewables is about using what’s near,” he says. “Biomass if near a forest, wind power if near a wind farm, solar power if in a solar area, and so on. For many existing distillers it’s about thinking of what’s least disruptive.”
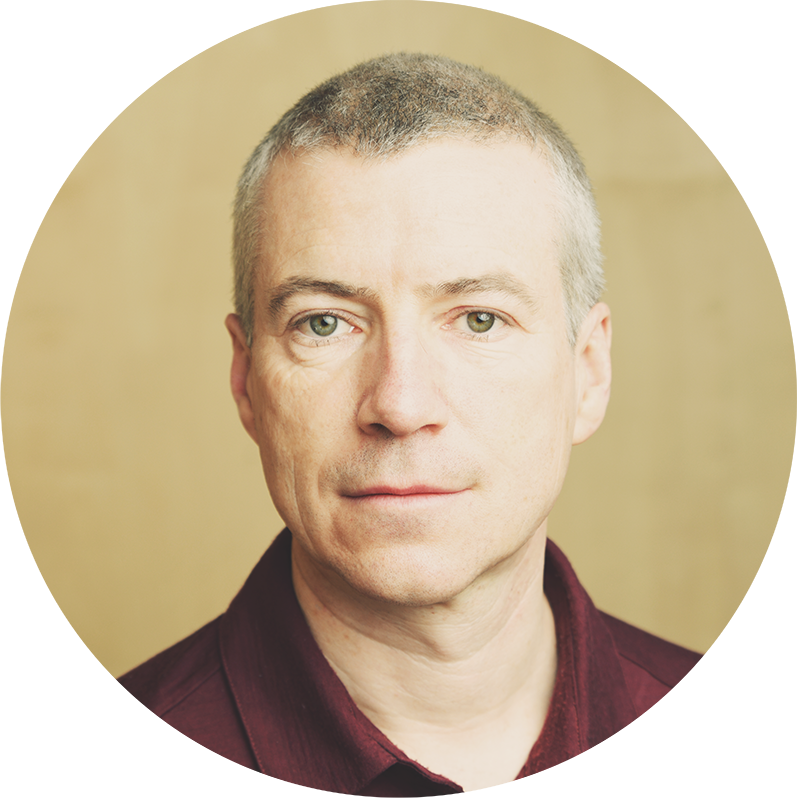
“Broadly speaking, it takes around one litre of fuel oil to produce each litre of pure alcohol. And there is a lot of spirit made in Scotland”
GARETH ROBERTS
“Renewables is about using what’s near. Biomass if near a forest, wind power if near a wind farm, solar power if in a solar area, and so on. For many existing distillers it’s about thinking of what’s least disruptive.”
GARETH ROBERTS
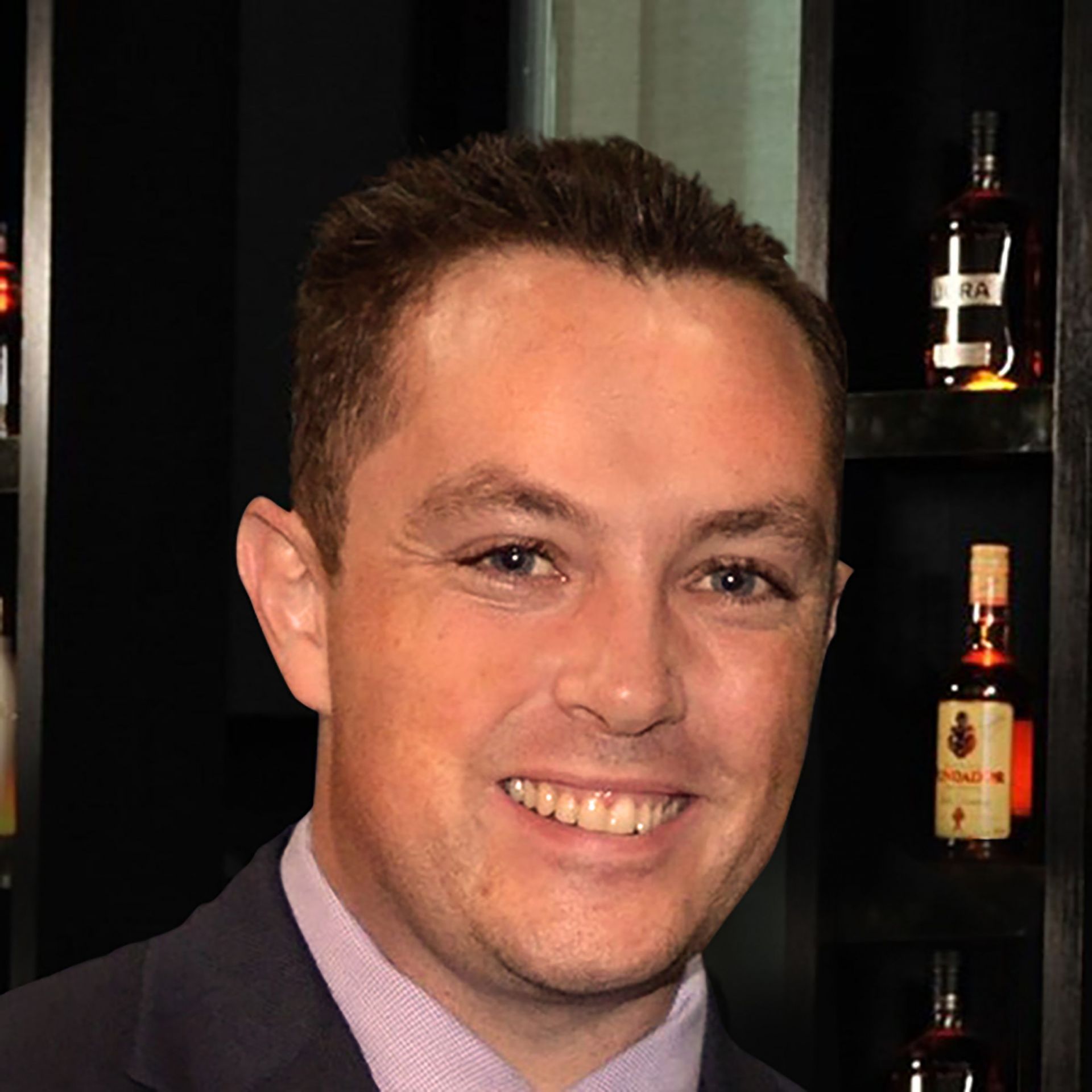
“We can’t sacrifice character for energy. If you’re starting to build a distillery from scratch, you can explore alternatives. But for us with existing distilleries it wouldn’t make sense to rip out all our equipment – the carbon impact wouldn’t be good! ”
SHANE HEALEY
TRYING AND TESTING
Looking to the future and the goal of carbon neutrality, Shane Healy notes that “Hydrogen gas is another energy option. One project is based in Peterhead, near Aberdeen – Acorn Hydrogen – and they are working with the SWA. They are getting lots of support from the Scottish Government and from industry, and will be producing in the next five years. The Cromarty Firth – where our Dalmore distillery is located – is aiming to be a ‘free port’ [where normal tax and customs rules do not apply] and a green hydrogen project is part of that.
“The SWA is really interested in hydrogen, but it’s like solar and wind were 20 years ago – it’s not yet tried and tested. We’re also evaluating heat pumps, which is very exciting. The Scottish Government set a target of being carbon-neutral by 2045, but as a company, Whyte & Mackay wants to achieve it by 2030.”
Douglas Murray, lead technology innovation manager distilled spirits for Diageo, says: “We have several plants that use our co-products to generate renewable energy through combustion of biomass and biogas, which in turn is used directly as steam in the distillery or to make electricity.
“All of our distilleries use 100 per cent renewable electricity generated from wind and we have also been trialling 100 per cent renewable liquid biofuels at some of our distilleries, too. As you would expect, we have active groups constantly looking at future technology. These include tidal power, hydrogen gas generation, energy storage and optimising our capability to use co-products to generate energy.”
KEEPING THE SPIRIT’S CHARACTER
Consistency is essential to every distillery’s production process, with oft-told stories of worn-out still parts being replaced with the same dings and dents to ensure nothing could alter the spirit’s character. When you start talking about alternative fuel sources and new equipment, that’s enough to make seasoned distillers get a case of the jitters.
“It’s vital that we don’t affect spirit character,” says Shane Healey. “We can’t sacrifice character for energy. If you’re starting to build a distillery from scratch, you can explore alternatives. But for us with existing distilleries it wouldn’t make sense to rip out all our equipment – the carbon impact wouldn’t be good!
“We prefer to optimise the existing equipment for as long as we can. That’s surely best. If someone says knock down your house and live in a tepee, you wouldn’t do it. But if you were starting from scratch, maybe a tepee is a cool idea.”
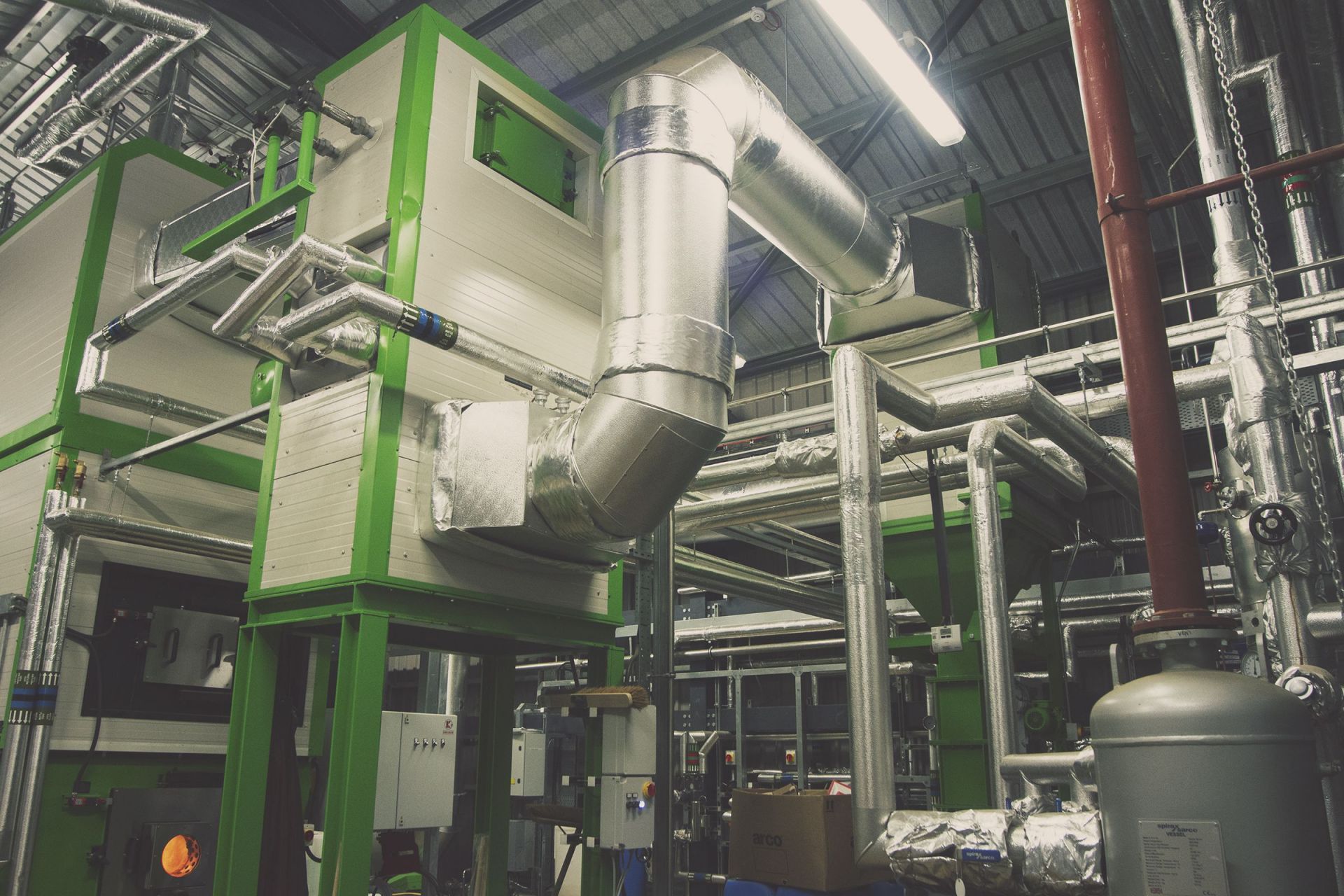
ABOVE: Nc’nean distillery’s biomass generator. Image courtesy of Organic Distilleries
A BLANK SLATE
But what if you are starting from scratch? That’s where architect Gareth Roberts is able to champion solutions to carbon elimination.
“Distilling will be carried out using low pressure, low-temperature systems,” he says. “Thermal fluids have been used for years in pharmaceutical, brewing and refinery plants, and by using them within a distilling system based around a hot well – a large thermal store – alternative fuel sources can be used which are generated locally. The resources of each area can be used to heat the hot well at the heart of the process. This central point also acts as a heat sink for heat which is reclaimed through the process rather than being wasted, as is the case at conventional steam-based distilleries.”
In a new low-temperature distillery, however, all of the production equipment is likely to be non-conventional, with Gareth suggesting that it may mean “smaller mash tuns, numerous small washbacks and smaller pots stills, all running more continuously. The replacement of steam distilling is a huge hurdle for established distillers who understandably resist any change which could impact upon the established and closely guarded character of the spirit. But think back to the 1970s, when direct-firing of stills was replaced with kerosene.
“Pot stills had rummagers to stir up the gloop in the base of the still,” says Gareth. “The change to steam pipe heating had a huge impact on the character of the spirit. However, it made things easier, so that change was embraced. This new challenge – indeed any switch to low-carbon – is going to be complex and possibly unsuccessful. There is so much expensive equipment in place that making the switch to new methods is going to prove extremely costly.”
LOSING MOMENTUM?
Given the uncertain social and economic times we’re living through, is it likely that some potentially expensive environmental strategies will quietly fall by the wayside, and momentum towards a green distilling future will be lost?
The SWA is adamant that despite the coronavirus pandemic, the whisky industry’s commitment to reducing its environmental impact continues.
Gareth Roberts is also optimistic. “I don’t think Covid-19 will have an impact upon the adoption of carbon reduction. I don’t think that’s the case at all,” he says. “The bigger distillers are cash rich and Covid-19 had just quietened the visitor centres. For the new distillers it is a part of their founding principles – or it should be.”
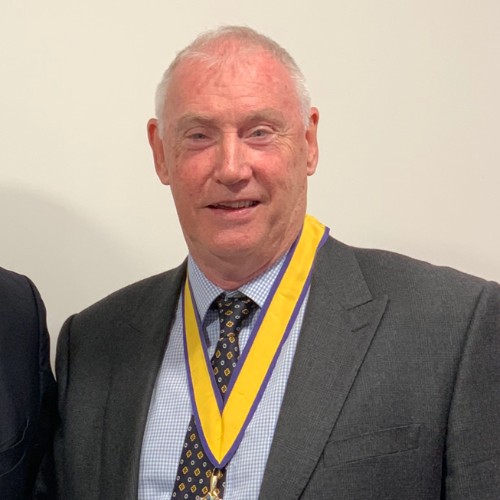
“We have active groups constantly looking at future technology. These include tidal power, hydrogen gas generation, energy storage and optimising our capability to use co-products to generate energy”
DOUGLAS MURRAY